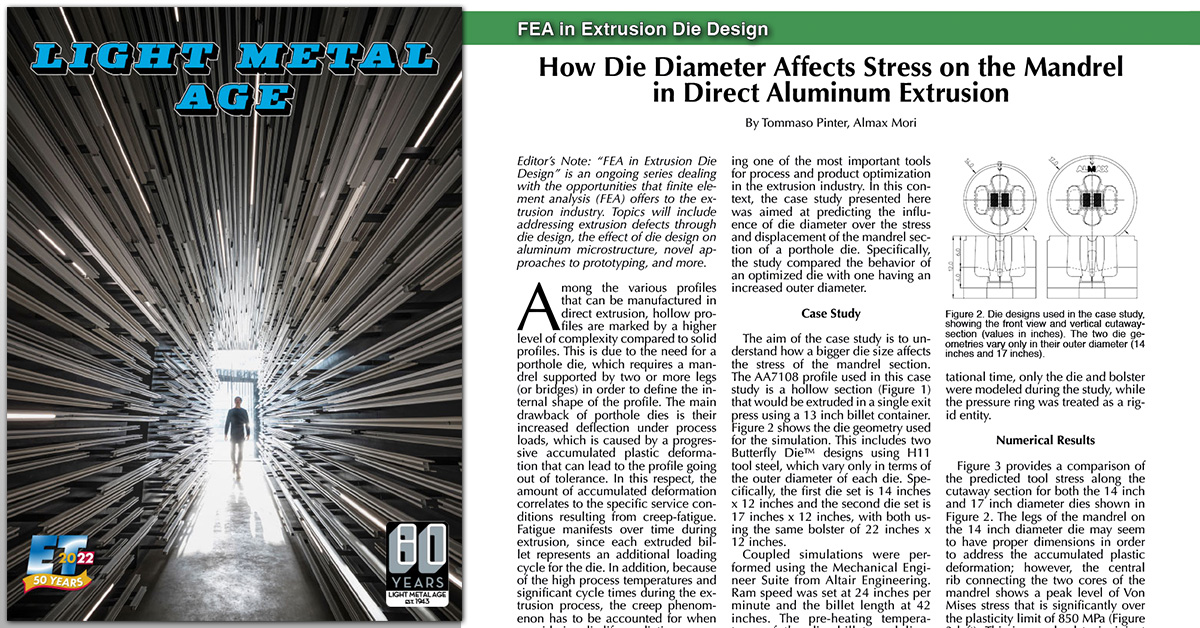
How Die Diameter Affects Stress on the Mandrel in Direct Aluminum Extrusion
Abstract
Among the various profiles that can be manufactured in direct extrusion, hollow profiles are marked by a higher level of complexity compared to solid profiles. This is due to the need for a porthole die, which requires a mandrel supported by two or more legs (or bridges) in order to define the internal shape of the profile. The main drawback of porthole dies is their increased deflection under process loads, which is caused by a progressive accumulated plastic deformation that can lead to the profile going out of tolerance. In this respect, the amount of accumulated deformation correlates to the specific service conditions resulting from creep-fatigue. Fatigue manifests over time during extrusion, since each extruded billet represents an additional loading cycle for the die. In addition, because of the high process temperatures and significant cycle times during the extrusion process, the creep phenomenon has to be accounted for when considering die life prediction. Die vendors are required to manufacture porthole dies capable of producing a required profile section within tight tolerances while achieving high production rates, as well as with the shortest front-end defect and the lowest knock-off rate. Last but not least, die life is also very important, as it directly influences the transformation cost of extrusion. During the die engineering phase, accurately estimating tool stress under load makes it possible to predict whether or not a mandrel might be subject to permanent plastic deformation. This is also important for optimizing die geometry to achieve the lowest peak stress on mandrel legs in order to optimize the operating life of the die. The most effective way to predict the tool stress of a die and, thus, its operating life is through the implementation of FEA, which is becoming one of the most important tools for process and product optimization in the extrusion industry. In this context, the case study presented here was aimed at predicting the influence of die diameter over the stress and displacement of the mandrel section of a porthole die. Specifically, the study compared the behavior of an optimized die with one having an increased outer diameter.